Our innovative GETC: AET/ABET NQF 1 learnership [SAQA] facilitates learning through practice. It is underpinned by the four important pillars that support any formal and structured workplace training programme. These include “purpose”; “curriculum”; “educational practice”; and “theory of knowledge”.
An education at NQF 1 is the bedrock of any workplace curriculum. Novices learn basic education skills while performing simple tasks in the workplace. As their proficiency gradually improves, they take on more complicated tasks and curricula. Certainly, a GETC: AET/ABET NQF 1 learnership does not only prepare employees for further training on the NQF [https://www.saqa.org.za/level-descriptors-for-the-south-african-national-qualifications-framework/]. It also equips them with the skills that they need to excel in companies’ own inhouse training programmes.
A case in point is the many competent machinists who have learnt their trade by participating in inhouse training programmes. This is an emerging trend in the industry. Steadily fewer employees are receiving formal schooling in the machinist trades. Instead, more machining businesses are increasingly training capable, reliable and motivated employees themselves. However, there are still companies that enrol their employees on formal machining courses, such as SAQA. This training is on the next band of the NQF. Three more courses enable employees to reach NQF 5.
Today, CNC machines can be found in just about every factory. They are deployed in small “job” shops in rural areas through to large “smart” factories in major urban nodes. This is considering the many benefits that they provide, not least of which are speed, accuracy and efficiency. However, they need to be operated correctly to avoid “crashing” them. This can result in high costs, including the price associated with repairs and downtime. Many companies still incorrectly assume that technology will address their skills gaps. The opposite is true; it is actually widening them!
GETC: AET/ABET NQF 1 learners
Many of these machinists started their careers as GETC: AET/ABET NQF 1 learners. Oftentimes, existing employees who perform general and mundane work are recruited to the learnership because they demonstrate potential. Then there are those many machinists who were initially recruited as unemployed individuals. Many manufacturers prefer this approach because they can “mould” these individuals into model employees. Young and energetic, they also learn quickly and bring fresh thinking to teams.
These employees started working as operators in machine shops while studying GETC: AET/ABET NQF 1 fundamental, core and elective subjects.
Recruited without any formal education in machining, operators are usually the lowest-ranked team members in machine shops. They simply load parts into CNC machines and remove the machined components for assembly. Two or three of these workers are usually assigned to a line, consisting of many CNC machines. They move from one machine to the next performing these functions during their shift. In addition, they perform general manual tasks at each machine and some cleaning work. In this way, they start familiarising themselves with companies’ systems and procedures.
GETC: AET/ABET and work experience
Equipped with GETC: AET/ABET NQF 1 skills and solid work experience, our clients can start moving these employees into other more critical roles. In this way, they can start filling the gaps as identified in their workplace skills plans. Refer to The Compiling of Workplace Skills Plans and Annual Training Reports Course – Labour Guide South Africa.
They usually start by moving them to different workstations. Thereafter, the most enterprising employees are considered for promotion to “quality gate inspector”. These employees inspect every part that comes off the production lines. This work is not too detailed, mainly involving visual and tactile inspection for surface roughness. Sometimes these operators may have to use gauges. The numeracy skills that employees learnt by attending maths literacy classes are sufficient for this type of work. Their reading, writing and active listening skills also enable them to follow basic instructions correctly. Furthermore, they have the confidence to speak up and ask for help when they do not understand what to do.
Having gained sufficient experience at this level, employees can be developed further, advancing from quality gate inspectors to “line keepers”. Line keepers are also involved in quality control, but they shoulder more responsibility. By sampling components, they determine whether their precision is within an acceptable range. This information is used to establish, for example, when tools inside CNC machines need to be changed. In this way, the required tolerance levels can be maintained. Line keepers also undertake machine inspection and troubleshooting when machines break down. In this way, they start learning the ins-and-outs of correctly maintaining these machines. Core maintenance tasks are imperative. Bear in mind the high cost of an unexpected CNC machine breakdown. It can be five times more expensive than a proactive annual maintenance plan!
GETC: AET/ABET graduates better prepared
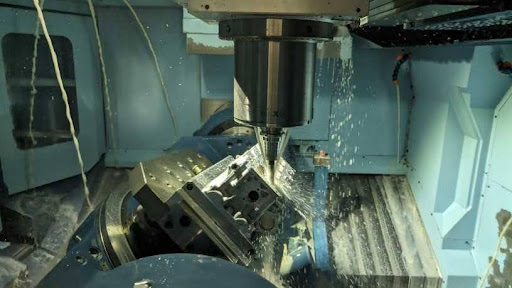
By this stage, GETC: AET/ABET learning graduates are better prepared for further learning.
While they are completing their training, employees will usually be assigned “sparemen” duties. They gain important experience while standing in for absent team members. Meanwhile, they also work with their manager in managing the lines. The tasks at hand include reporting; updating data; and involvement in total productive maintenance. Furthermore, they help to implement machine problem countermeasures, including parameter control.
One they have completed their training and have sufficient experience, “sparemen” can be prepared to assume leadership roles. Employees who have completed GETC: AET/ABET NQF 1 have already learnt many “soft” skills that most line managers must possess. First-and-foremost, they have sound communication skills. This enables them to convey instructions clearly and concisely. In this way, their teams know what is expected of them at all times. Importantly, effective communication also fosters trust and understanding and promotes cohesive team environments.
Furthermore, attending GETC: AET/ABET learning classes and working in a factory setting, employees have developed their problem-solving skills. This is complemented by good time keeping and an ability to manage conflict. Putting these to use, they can keep production lines running seamlessly.
GETC: AET/ABET facilitates further learning
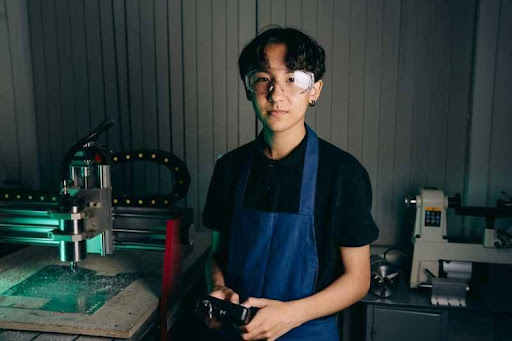
Now, let’s look at how GETC: AET/ABET NQF 1 training facilitates further learning in the workplace.
Our learnership is not just about teaching “soft” skills. Certainly, this learnership is very effective in integrating these skills into blue-collar work. However, the skills we teach are also the foundation upon which “hard”, job-specific or technical skills are developed. These include language, literacy and communication, as well as mathematical literacy skills. Considering their importance, these are fundamental learning areas of our GETC: AET/ABET NQF 1 learnership.
Employees who have been identified for career advancement, need to be able to read fluently. This includes an ability to read technical instructions and safety procedures for meaning. These procedures are presented in machine manuals and manufacturers’ safety documentation [https://cdn.sick.com/media/docs/8/78/678/special_information_guide_for_safe_machinery_en_im0014678.pdf]. Employees will already start referencing this information during training and use them throughout their careers.
Moreover, as employees learn their trade, they will have to read charts and graphs. These are also contained in vast technical documents, such as All HOLZ-HER catalogs and technical brochures (directindustry.com). Furthermore, employees will be expected to compare diagrams to the machines that they are using. This is in addition to making sense of flowcharts. These, for instance, demonstrate the correct loading of CNC machines. Notably, incorrect loading is one of the lead causes of defective components in machine shops. Alignment with the work-holding chucks requires absolute precision!
GETC: AET/ABET bridges skills gaps
Developed with industry, our GETC: AET/ABET NQF 1 learnership bridges skills gaps on factory floors. Considering the rate of technology acceptance and uptake in these working environments, blue-collar workers must be fluent readers. Therefore, our language, literacy and communication studies focus on developing vocabulary, fluency and comprehension skills. These are taught via SAQA, which counts six credits towards this particular learning area, alone.
Our clients want employees who confidently approach reading tasks. They activate their background knowledge before reading and know why they are reading company documentation. Furthermore, they can predict and choose appropriate strategies for passages of text. Employees must also be able to summarise major ideas and recall supporting details; make inferences; and paraphrase. In addition, they can focus their complete attention on reading without being distracted.
However, good readers can also use appropriate word-decoding skills and monitor their comprehension during and after reading. They also have an ability to anticipate and predict meaning of words. They do so by using context clues and other strategies learnt during language, literacy and communication classes. Furthermore, they know how to create visual and sensory images from text. This is in addition to possessing a large repertoire of strategies to help understand unfamiliar passages.
GETC: AET/ABET teaches writing skills
GETC: AET/ABET NQF 1 also teaches robust writing skills [SAQA]. This learning area contributes six credits towards language, literacy and communication studies. Employees will use this skill widely to complete course assignments and to write tests and examinations.
However, writing is also an important workplace skill. At the most basic level, factory workers need to use the correct grammar, punctuation and terminology to complete work documents. They may even be required to contribute towards the writing of documents and even edit them. This is as they climb the corporate ladder to the top.
Yet, effective communication is more than just the written and spoken word. Therefore, language, literacy and communication studies also teach the importance of non-verbal behaviours in the workplace. Developing active listening skills is also a focus area of this subject. These skills are taught via SAQA, which counts six credits towards the qualification. On a daily basis, employees will use these skills to interpret verbal and non-verbal behaviours. This is to enhance communication with co-workers, higher-ups, suppliers and clients. They also use them to obtain and clarify information and interpret it. As employees advance, they will also use information to compile tables, charts and figures to support written and oral communication. In leadership positions, they will also explain written organisational policies and rules and procedures to help employees perform their jobs.
GETC: AET/ABET teaches relevant numeracy
Importantly, GETC: AET/ABET NQF 1 also teaches mathematical literacy, relevant numeracy for the factory floor.
Novices will never succeed in technical training if they do not have strong foundational numeracy skills.
A large part of machining, for example, involves measuring. The dimensions of particular parts are usually stated within a certain tolerance limitation.
Therefore, managers of these factories are reluctant to employ people with poor mathematics skills. Unfortunately, many had to learn the hard way. There have been instances where unskilled and low-skilled employees have confused addition and subtraction when measuring.
This is an extenuating circumstance. However, employees who do not possess strong numeracy skills will struggle to grasp certain concepts associated with machining. A case in point is geometry, which is adequately covered by SAQA. This study counts five credits towards GETC: AET/ABET NQF 1’s mathematical literacy, alone.
Certainly, measurement is also a significant focus of our learnership [SAQA]. As one of our clients said, “Measurement is the guarantee of quality!” In her factory, employees use measurement to check all the work that they do. Work is considered incorrect if it has been inspected inappropriately. This is even the case when it was actually done correctly – such is the weight given to measurement in this workplace.
However, measurement in machining is more than just length or diameter. It also has a geometric characteristic that needs to be understood. If employees grasp this, they will be able to learn other factors of the trade more easily. Then, they are ready to start learning about machine tools, coolants and CNC machine brands.
GETC: AET/ABET improves manufacturing competitiveness
In this way, GETC: AET/ABET NQF 1 improves manufacturing competitiveness in the country.
Mathematics education in particular is one important indicator of the competitiveness of a country’s manufacturing industry. Yet, the quality of our mathematics and science education is ranked 128 in the 2071 Global Competitiveness Data. This is only better than 10 other countries that participated in the study [https://www.thedtic.gov.za/wp-content/uploads/publication-Facts_Figures-Manufacturing.pdf].
As a country, we are still struggling to find competent operators to keep our CNC machines running. Yet, the technology has already undergone major advancements that call for even more sophisticated skills. For example, our international counterparts are already integrating automation and robotics into CNC machining. This requires a workforce that is both versatile and tech savvy.
Learn how Triple E Training can help you to develop these skills. www.eee.co.za